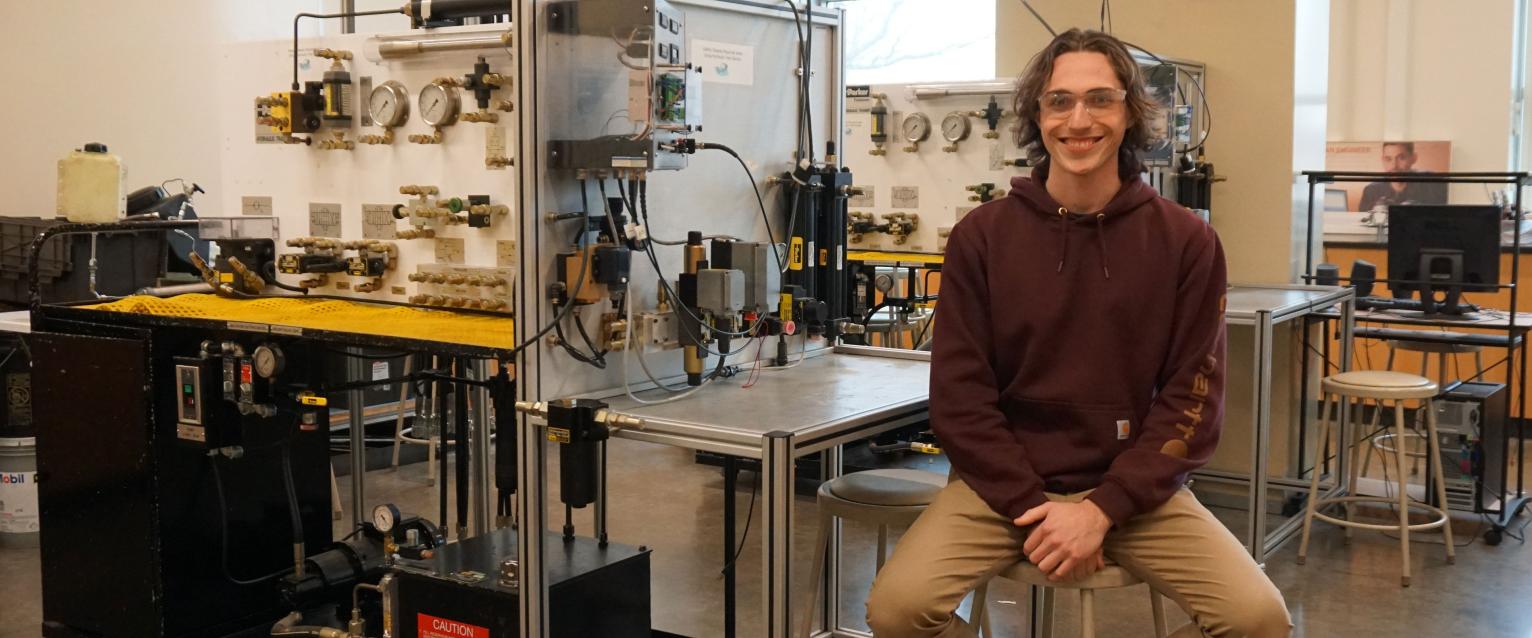
Motion and Control Laboratory
Supported through ongoing grants from Parker-Hannifin Corporation since 2003.
Th Parker-Hannifin Motion and Control Laboratory at Âé¶¹´«Ã½ trains undergraduate and graduate engineers in hydraulic, pneumatic and electromechanical systems engineering. The lab is focused on hydraulic system engineering experiences and Âé¶¹´«Ã½ exposure to pneumatic and electromechanical systems.